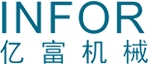
东莞市亿富机械科技有限公司
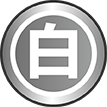
已认证
东莞市亿富机械科技有限公司
已认证
1、固态电解质:目前技术路线未定,各有优劣
2、硫化物:离子电导率最高,发展潜力巨大
➢ 硫化物电解质具有理想的离子电导率(媲美液态电解质),良好的电极材料兼容性(较宽的电化学窗口),是目前最理想的固态电解质之一,在全固态电池中发展潜力最大。但是亟待解决的问题多多:
➢ 1)界面不稳定,容易发生副反应造成阻抗变大;
➢ 2)碱性和水性环境下极易发生化学反应生成硫化氢;
➢ 3)稀土金属的添加大幅提升了加工成本和材料成本。
➢ LGPS型和硫银锗矿型离子电导率高,同时硫银锗矿型SE具备低成本高稳定性特点,具备较好的发展前景。
3、硫化物:目前面临原料及电池多方面量产难题
➢ 1)关键固态电解质材料的大规模生产和降本:包括大规划量产(克级到吨级),纳米级别制备(um级别做到nm级别),连续化生产以及成本控制;
➢ 2)极片层面量产难题:包括混料(正负极材料+固态电解质混料),匀浆制片(湿法正负极的匀浆问题),干法电极生产
➢ 3)电池层面量产难题:电池生产,装配,以及空气湿度控制
➢ 4)终端应用:能量密度提升,电池容量保持,电池循环寿命
4、硫化物:如何实现原材料大规模生产是首要难题
➢ 硫化物固态电解质目前面临大规模量产难题:原材料的一致性,粒径控制问题,同时硫化物SE对空气/水敏感,运输连接的密封也至关重要;
➢ 一般来说,硫化物电解质制备方法可以分为三类:1)固相反应法:按照化学计量比加入原材料混合组成前驱体材料,前驱体材料加热到熔点熔融,之后将样品冷却到室温得到电解质材料,期间反应条件苛刻,同时直接高温下锂硫挥发,容易产生杂项;2)机械球磨法:在高速球磨的过程中,原料颗粒在冲击中实现碰撞扩散及反应;3)液相法:以有机溶剂为介质合成硫化物电解质,合成的电解质颗粒小且一致性好,但溶剂一般为有毒溶剂,同时液相法生产出来的硫化物电解质电导率略低于固相法。
5、硫化物:如何低成本生产是次要难题,核心在硫化锂
➢ 硫化物电解质原料一般为硫化锂,五硫化二磷及氯化锂,其中硫化锂为主要原料。
➢ 硫化锂在自然界并不稳定,在空气中易吸收水蒸气发生水解,放出剧毒硫化氢气体,可被酸分解放出硫化氢,可与硝酸剧烈反应;电池级硫化锂与工业级的区别在于产品的纯度和粒径要求不同。
➢ 由于目前硫化锂售价高昂,且空气稳定性问题难解决,制备的时候需要比较好的空气保护,导致硫化物电解质量产难度在于如何实现硫化锂的大规模低成本量产。
6、硫化物:上市公司工艺各异,液相法成本相对较低
➢ 主流上市公司布局硫化锂的工艺路线各有千秋,主要集中固相法、液相法以及碳热还原法,其中以有研新材、容百为代表的使用固相工艺制备硫化锂,厦钨、天赐等使用液相工艺制备硫化锂及硫化物电解质,恩捷股份、容百采用碳热还原法制备硫化锂,并采用固相工艺制备硫化物电解质。
➢ 从成本角度来看,液相法制备硫化锂存在一定的成本优势,但目前仍处于量产前期,后续成本下降情况需进一步验证。
7、硫化物:硫化锂目前成本占比70%+,后续降本空间大
➢ 以高能时代5Ah全固态电池估算,目前1Wh全固态电池的BOM生产成本在1.66元/Wh,其中假设硫化锂单吨售价在300万元/吨,对应硫化锂生产成本占电池生产成本75%左右,未来随着国产硫化锂技术逐步突破,假定硫化锂价格下降至30万元/吨,对应硫化物固态电池的BOM成本下降至0.54元/Wh,降本空间较大,未来有望实现与锂电池平价。
8、硫化物:电池电极、电解质膜生产是第三大难题
➢ 电池复合电极、电极膜生产难题:硫化物固态电解质生产后,电池极片选择复合极片,由活性材料、导电添加剂和SE组成,中间会存在界面问题,导致电极内阻增加,容量下降,如何克服内阻和容量问题是后续改进重点,复合极片制备中物料混合后,如何和集流体紧密粘连也是难题所在。
➢ 硫化物电池大规模生产:难点在于干法电极、致密化加压、特定环境装配,其中干法电极难度在于粘合剂纤维化,目前合适的纤维化设备(例如高速气流吹扫、螺杆挤出机、轧机)仍在开发中;同时电极需要紧密的固体-固体接触,等静压300MPA是后续难题;最后硫化物SE对空气/水敏感,SE材料制造可能需要封闭循环惰性气氛,电池制造期间需要更严格的干燥条件。
9、硫化物:产业链积极布局产能,产业化加速可期
➢ 产业链中从上游锂盐厂、中游材料厂以及下游电池厂均布局硫化锂及硫化物固态电解质生产,后续随着国产硫化锂生产壁垒突破后,硫化锂售价有望下降,带动硫化物固态电池产业化进展加速。
最新动态
更多
虚拟号将在 秒后失效
使用微信扫码拨号